Angular Forklift Safety System: Safezone EDGE
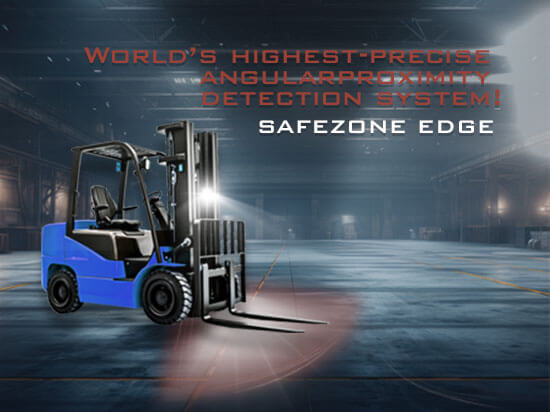
In the dynamic environment of warehouses and industrial facilities, it is well-known that forklift safety systems play a critical role. Conventional 360° forklift safety systems have been fundamental in reducing risks for an extended period. However, with the technological advancement of industries, the increase in personnel and equipment, and the shortened operation durations, safety systems have become more crucial than ever. This situation has revealed some efficiency limitations of conventional 360° forklift safety systems over time, prompting industries to seek more effective, efficient, and secure technologies.
Conventional 360° forklift safety systems face significant challenges for improvement
1. False alarms and prolonged slowdowns
False alerts and lengthy forklift slowdowns result from forklift collision warning systems misinterpreting environmental conditions or getting false real-time data for a variety of causes, including signal congestion. This condition disrupts smooth operations, causes process delays, wastes time, and reduces employee faith in safety technology.
2. Perceiving side-by-side movements of forklifts as danger
Most forklift collision warning systems struggle to identify side-by-side motions, which occur when forklifts move nearby or a person walks along a pedestrian path. This difficulty originates from these technologies' failure to effectively recognize such events. As a result, it disrupts workflow, reduces operational efficiency, and causes unnecessary forklift slowdowns. Operators who are regularly exposed to false alarms may grow desensitized and dismiss such warnings. This condition might lead to a decrease in employee faith in the facility's safety mechanisms and an increase in workplace safety concerns.
3. Primary challenges for companies requiring high-precision
Most forklift collision warning systems have limited infrastructure technology, which can prevent them from detecting obstacles or hazards in advance. Furthermore, companies that require high precision may encounter difficulties in selecting a system that meets their requirements due to the proportional increase in costs associated with the facility's size. This quandary can impede the attainment of desired efficiency. Restricted detection distances and low precision have the potential to increase workplace safety risks while decreasing operational efficiency. Forklift operators may encounter unexpected issues as a result of the system's failure to anticipate hazardous situations. As a result, operational efficiency may suffer, leading to costly financial and legal consequences.
The Answer is Safezone EDGE
The Safezone EDGE Forklift Collision Warning System addresses the challenges posed by forklift safety systems in industries, offering an innovative solution to businesses in a world where forklifts are indispensable, yet efficiency often decreases due to workplace safety measures. This system stands out among collision warning systems due to its UWB-based angular proximity and direction detection technology, designed to prevent potential accidents between machinery, pedestrians, and equipment. Safezone EDGE provides a fresh approach to enhancing safety without compromising efficiency in environments where forklift use is essential but productivity can be impacted by traditional safety solutions.
Safezone EDGE is a collision warning system that stands out for its plug-and-play technology, which does not require any infrastructure, unlike other systems. Operating on a "peer-to-peer" basis without the requirement for RTLS infrastructure, its most notable feature is its angular proximity and direction detection algorithm and UWB infrastructure. It can determine angular approach directions by correctly measuring forklift relative speeds, directions, and distances. This enables Safezone EDGE to identify potentially hazardous approaches between forklifts with more accuracy than other forklift safety systems, regardless of angle.
Furthermore, customizable virtual warning distances around the forklift allow for the same precision level as existing RTLS-based systems. These adjustable distance settings are especially useful in establishing efficient working environments for forklifts and pedestrians moving side by side. As a result, Safezone EDGE provides up to 100% more efficiency than conventional 360° collision warning systems, giving businesses a significant advantage in creating a faster and safer working environment.
SMART solutions for pain-points in conventional 360° forklift safety systems
Safezone EDGE distinguishes itself from other systems with its innovative solutions that bring a difference to conventional 360° forklift safety concepts. Wipelot's industry-leading expertise, a vision that successfully integrates customer expectations into products through robust R&D efforts, and continually evolving system algorithms have resulted in Safezone EDGE – a positioning technology with top-notch precision and low latency that offers higher efficiency without compromising on workplace safety standards.Dynamic distance detection
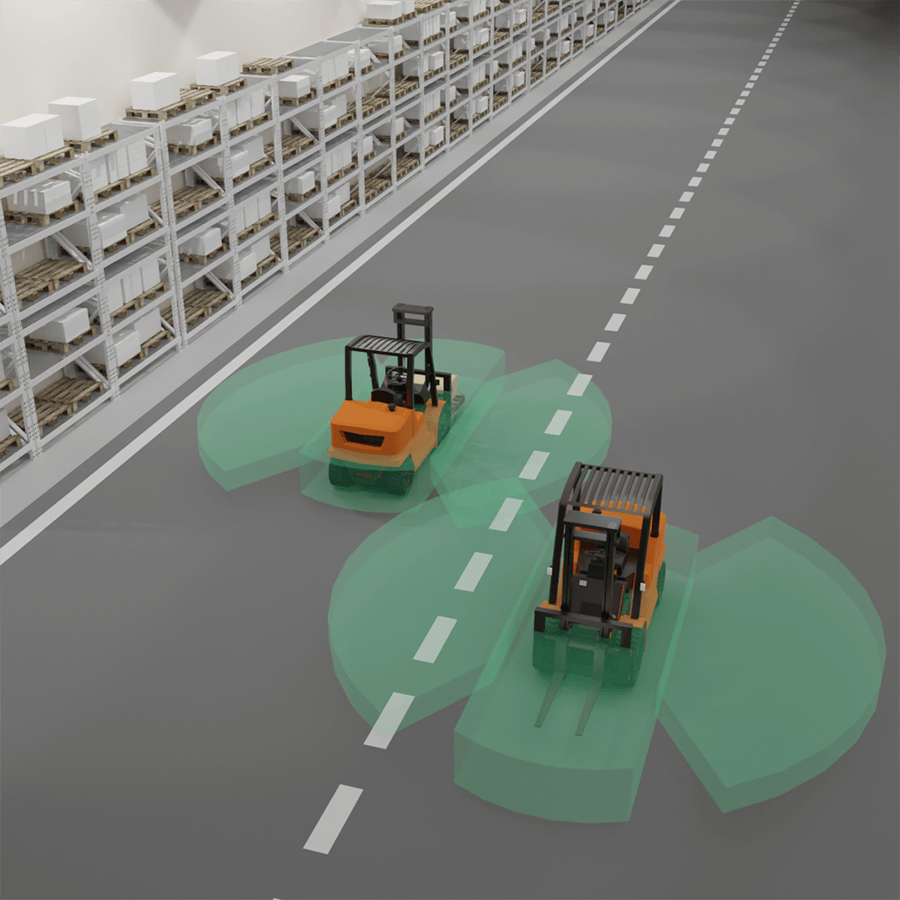
The dynamic distance detection feature of Safezone EDGE was developed as a solution to unnecessary and prolonged forklift slowdowns. The system, which slows down forklifts approaching each other dangerously, calculates the relative speeds and movement directions of the forklifts, executing the slowdown when necessary. Unlike conventional 360° forklift safety systems, this feature prevents unnecessary and prolonged slowdowns, preserving operational efficiency.
Sequential motion
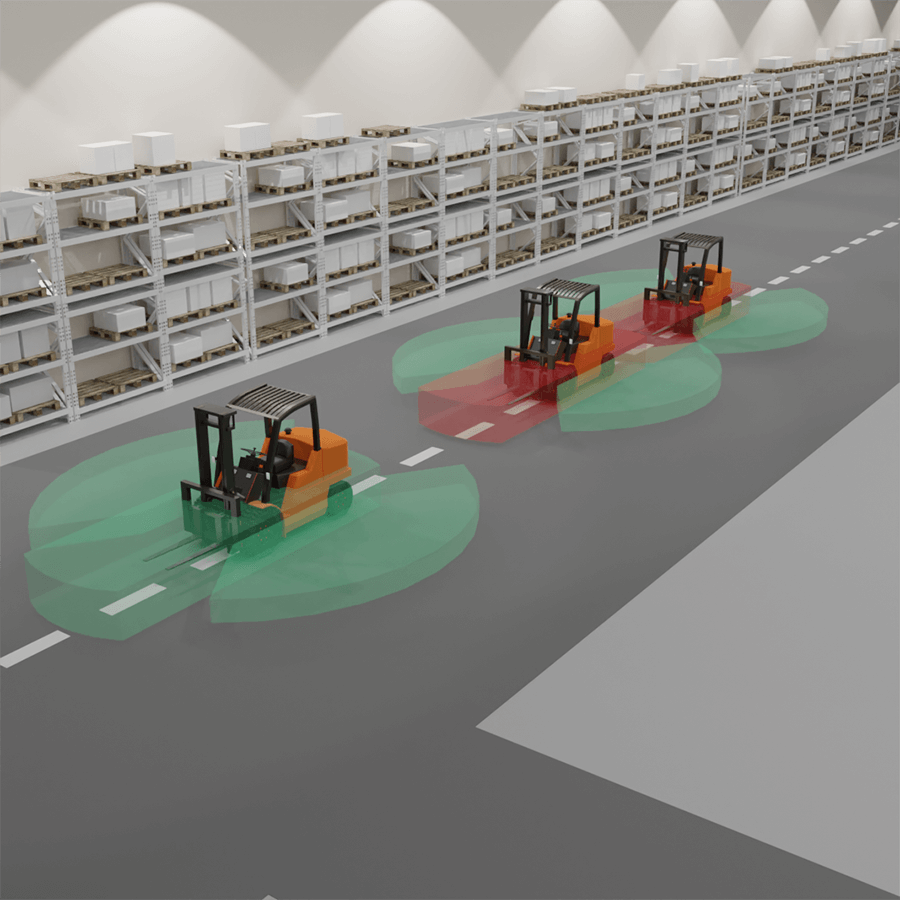
The sequential tracking feature of Safezone EDGE was developed to address the decreased operational efficiency caused by forklifts moving back to back. When there are no dangerous approaches or distance violations, this feature prevents unnecessary slowdowns, allowing multiple forklifts to move smoothly in sequence without compromising workplace safety, increasing the efficiency of intralogistics operations.
Parallel (side by side) motion
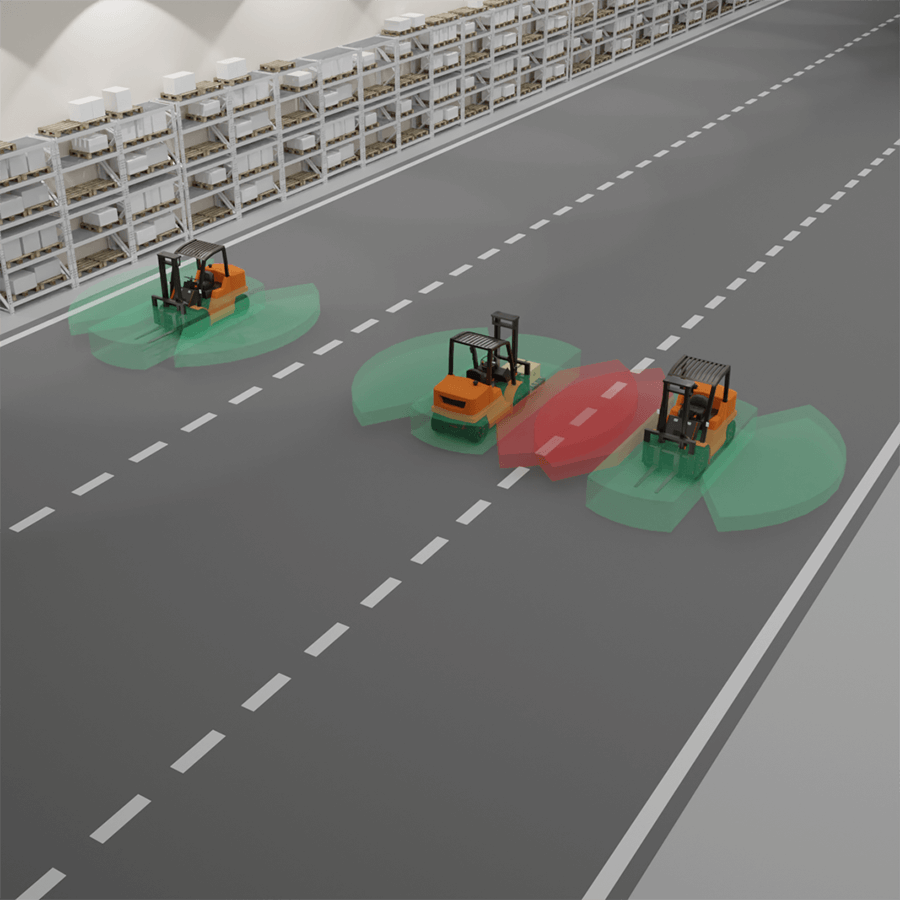
Vehicles moving side by side are frequently considered a potentially dangerous approach in conventional 360° forklift safety systems, triggering alarm scenarios. The Safezone EDGE algorithm detects approaching vehicles and initially slows them down. Then, calculating relative speeds and directional positions allows forklifts to move side by side up to 50 cm apart if desired. This feature improves operational efficiency by avoiding unnecessary slowdowns in intralogistics operations that involve parallel driving with no risk of collision or in areas where pedestrians walk on pathways separated by barriers.
90° proximity detection
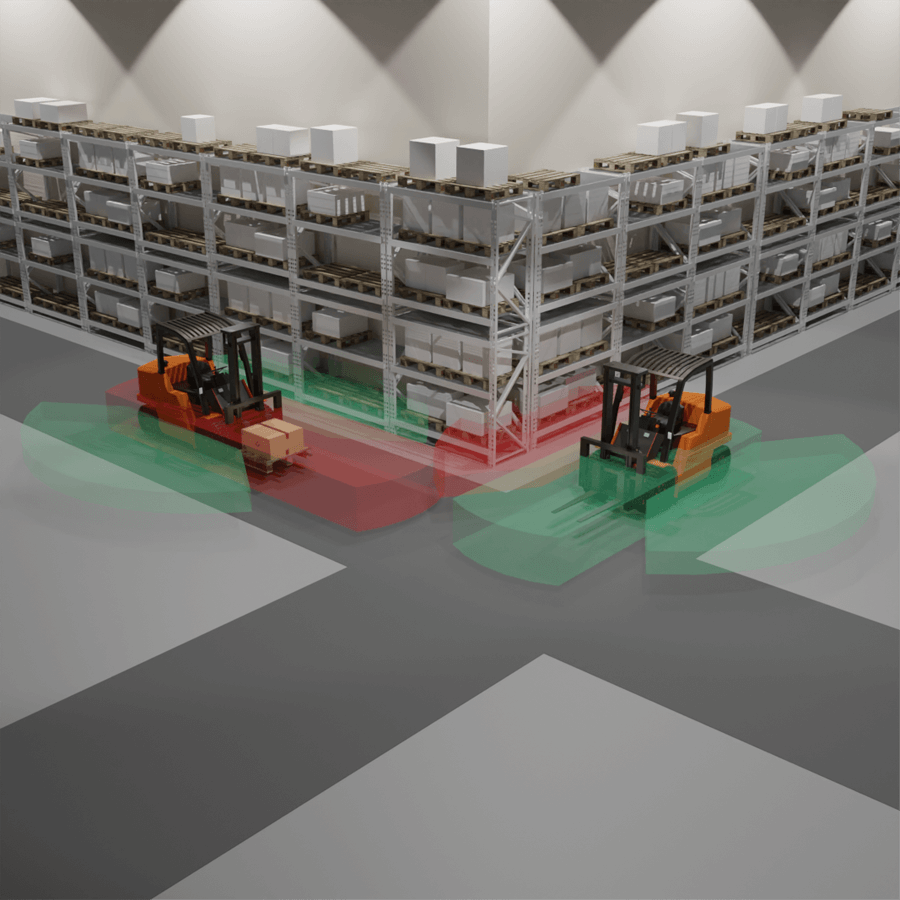
When two vehicles approach each other at a 90-degree angle from behind obstacles such as shelves, aisle ends, and intersections, Safezone EDGE detects potential collisions. It issues warnings and automatically slows down the forklift. While other collision warning systems may have similar features, they typically require additional hardware for each blind spot zone. That can cause significant cost increases, sometimes amounting to thousands of dollars.
Safezone EDGE, with its high precision and based on a closed-circle RTLS (Real-Time Location System) logic, eliminates the need for additional devices for 90-degree approaches or blind spot warnings thanks to its relative speed calculation algorithm. Compared to other forklift safety systems, this feature not only improves workplace safety but also provides more cost-effective solutions.
Impact detection
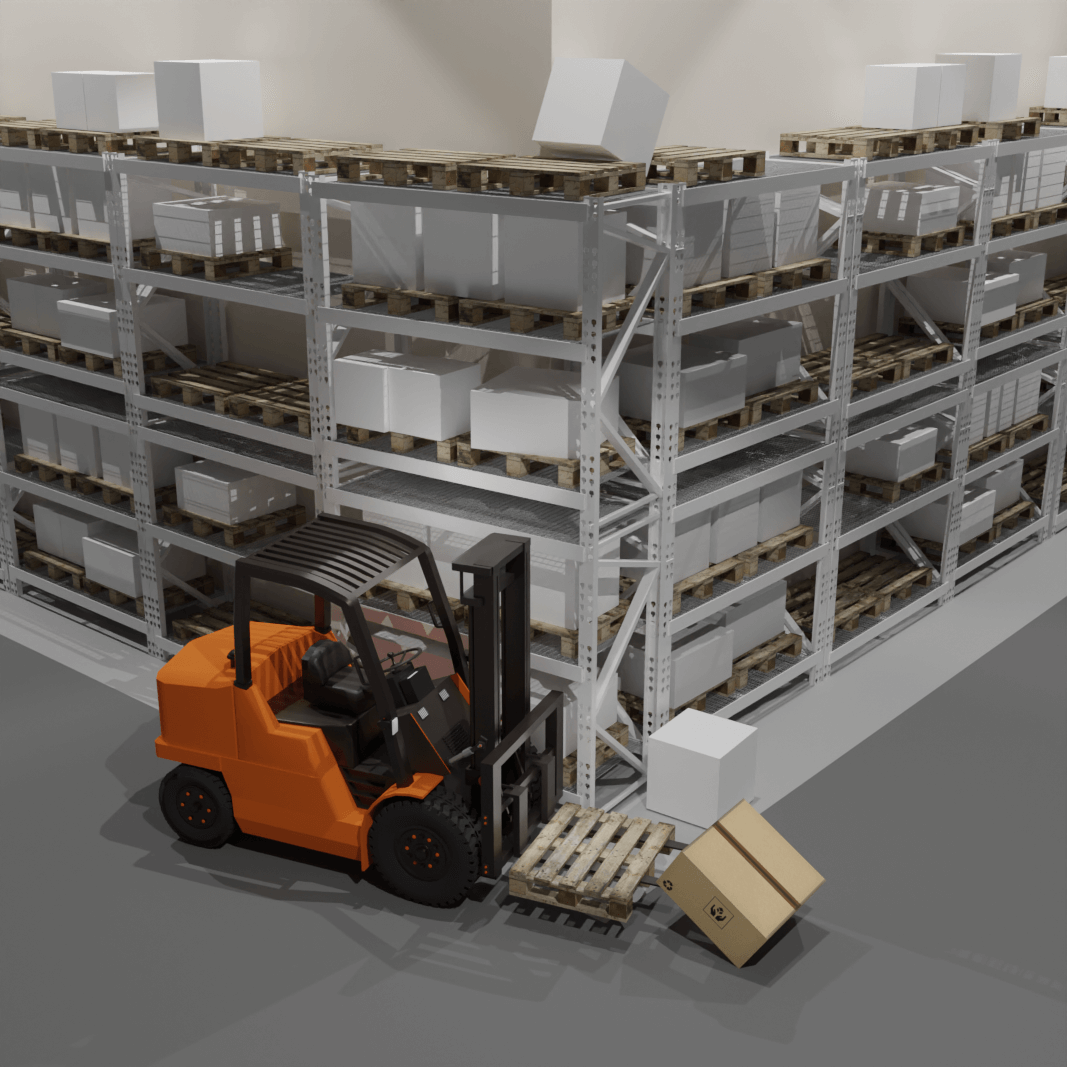
When a collision occurs, the Safezone EDGE collision sensor is designed to stop or slow the forklift. The system does not allow the vehicle to resume normal operation until it recognizes the card of authorized personnel and obtains their approval. The forklift can be used at full speed again after receiving approval from the authorized individual. The device's internal memory stores the impact for later review and analysis. This feature improves safety by requiring authorization for vehicle recovery and keeps a record of collision incidents for further review.
Advanced blind spot detection
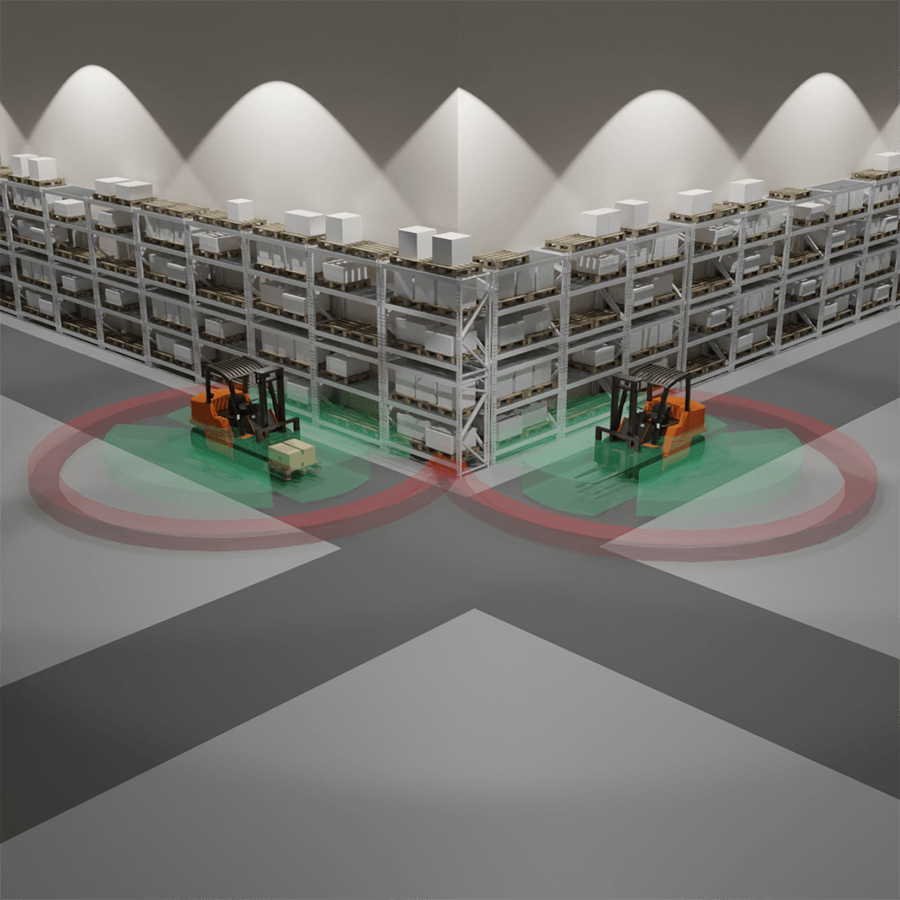
Forklift accidents caused by blind spots are one of the leading causes of injuries and high-damage incidents in facilities. Thick concrete walls, wide pillars, and buildings that divide zones of the facility might make forklift collision avoidance systems difficult to use because they interfere with signal transmission. Safezone EDGE uses a proprietary algorithm developed by Wipelot to detect potential hazards, offer warnings, and slow down vehicles without the need for additional equipment. This system effectively assures operational safety, especially in locations where data connectivity is limited, by recognizing the potential collision risk between two vehicles behind impediments such as concrete blocks and walls.
Proximity warning system for AGVs
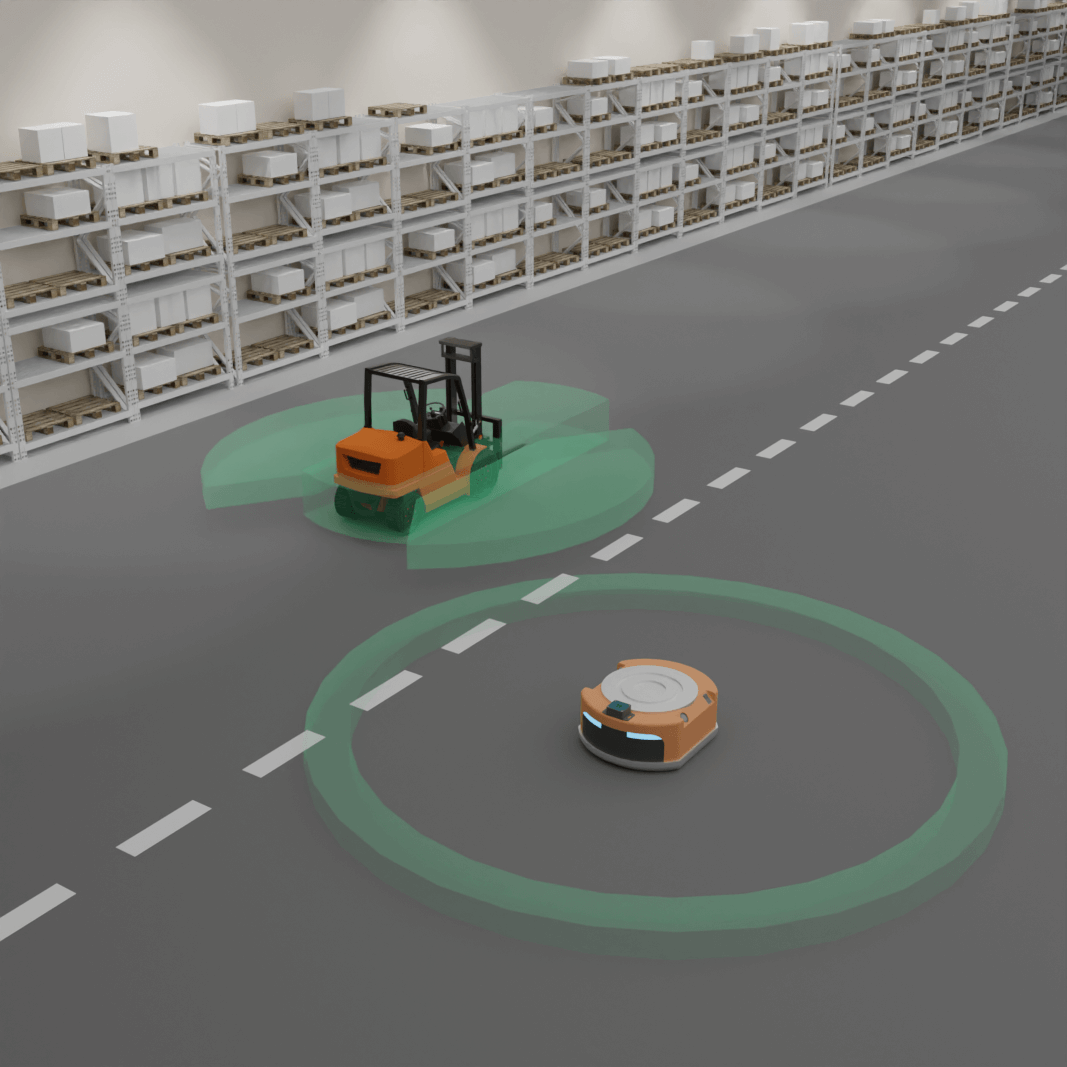
Safezone EDGE not only protects forklifts but also AGVs utilized in modern warehouses. In the event that forklift and pedestrian personnel approach AGVs in a harmful manner, specially developed battery-supported AGV mobile tags provide visual, aural, and vibrating alerts to operators and pedestrians. This allows for the early prevention of potential collisions.
Safezone EDGE Forklift Safety System goes beyond conventional 360° safety systems and provides an industry-changing solution. Safezone EDGE significantly improves forlift safety standards by innovatively addressing pain points such as collision avoidance, effective sequental movement, and advanced detection of collision risks. The advanced features of the system not only help to reduce workplace accidents but also improve operational efficiency. Improved productivity, reduced downtime, and a safer working environment benefit the industry. The ability of Safezone EDGE to integrate seamlessly into existing workflows, as well as its cost-effective approach, position it as a forward-thinking safety solution that meets the evolving needs of modern forklift operations.
Frequently Asked Questions about the Safezone EDGE Forklift Safety System
How does Safezone EDGE minimize false alarms in forklift operations?
Safezone EDGE uses angular proximity and direction detection algorithms powered by UWB technology to distinguish actual collision threats from routine movements. This significantly reduces false alarms caused by conventional 360° systems.
What makes Safezone EDGE effective for side-by-side and sequential forklift movement?
Unlike traditional systems that misinterpret parallel or sequential motions as hazards, Safezone EDGE accurately calculates relative speeds and directions. It allows forklifts to operate efficiently even when moving closely together.
How does Safezone EDGE enhance safety at blind spots and intersections?
Safezone EDGE detects 90° proximity approaches and blind spots without requiring additional sensors, using its closed-circle RTLS logic and relative speed algorithms to issue timely alerts and initiate slowdowns.
What is the role of Safezone EDGE in preventing high-cost impacts in warehouses?
The system includes impact detection sensors that stop the forklift after a collision. Operation resumes only with authorized personnel approval, and all events are logged, minimizing liability and downtime.
Can Safezone EDGE be used with AGVs and without infrastructure?
Yes, Safezone EDGE works on a peer-to-peer model without RTLS infrastructure. It also includes mobile tags with visual and audio alerts for AGVs, enabling compatibility and protection in hybrid vehicle environments.