Industrial Crane Safety and Positioning with RTLS
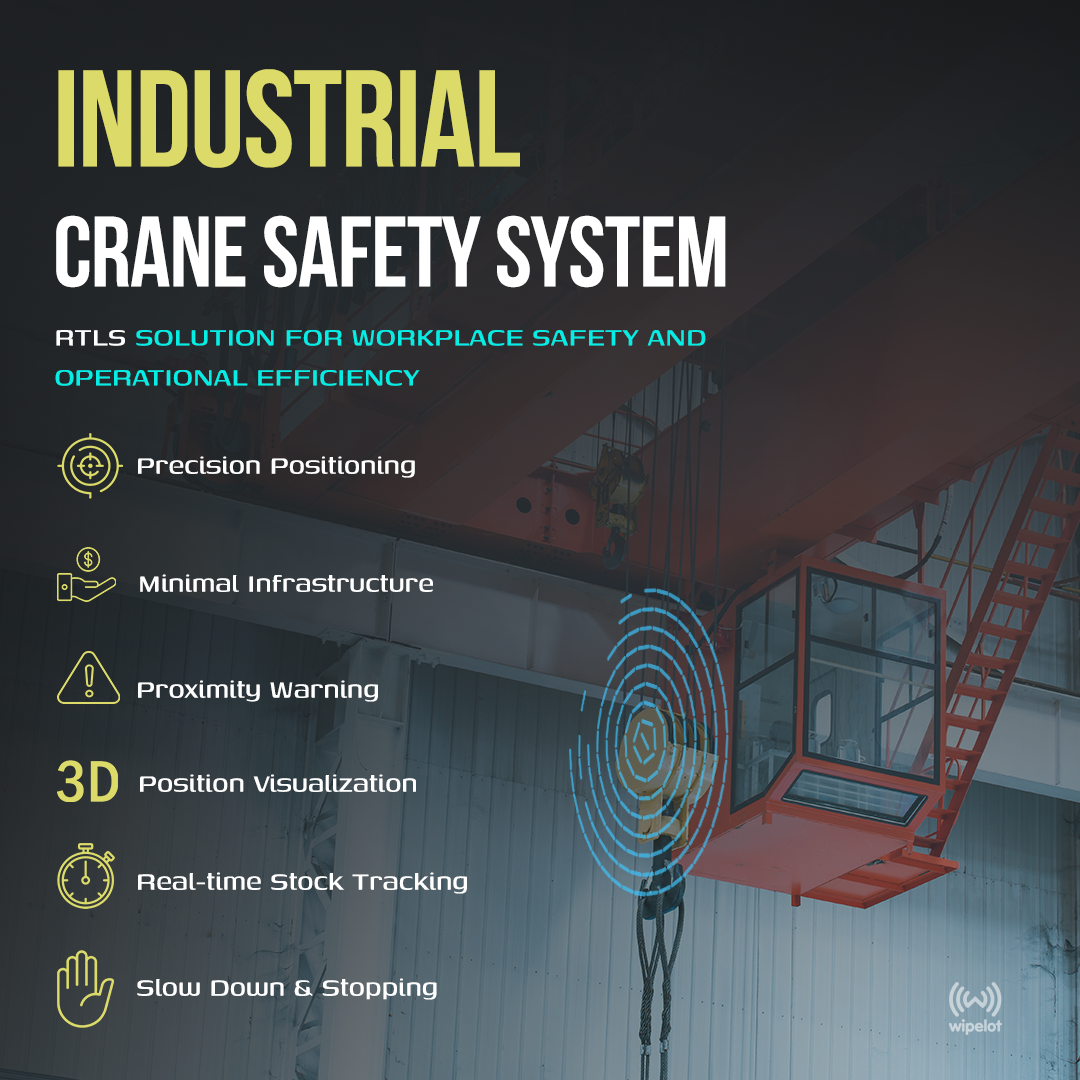
Industrial cranes are mechanical equipment that play a critical role in safely transporting heavy loads and ensuring the smooth operation of work processes. With their high lifting capacity and designs tailored to specific applications, industrial cranes are an essential part of industrial facilities. They enhance workplace safety and support operational efficiency across a wide range of industries, including heavy industry, steel production, ports, warehouses, and production lines.
Types of Industrial Cranes
Industrial crane safety is a key consideration in heavy load handling systems. Industrial cranes offer customized solutions tailored to the needs of various industries. These cranes aim to enhance operational efficiency by accelerating work processes while ensuring the highest level of workplace safety. Since each industry has unique requirements, numerous types of cranes have been developed based on lifting capacities, movement mechanisms, and areas of use.
Industrial cranes can be utilized across a broad range of applications, including heavy industry, steel production facilities, ports, transportation zones, warehouses, and production lines. Their versatility allows them to operate effectively in both indoor and outdoor settings. Equipped with modern technologies like real-time location systems (RTLS), these cranes incorporate advanced crane position monitoring systems and safety solutions to make work processes safer and more efficient.
The features and advantages of these cranes vary depending on the weight of the load to be handled, the physical characteristics of the work environment, and operational requirements.
Overhead Crane
Overhead cranes, also known as “bridge cranes,” are designed for transporting heavy loads in large spaces. These cranes can operate in both indoor and outdoor environments, with lifting capacities ranging from 30 tons (single girder) to 90 tons (double girder) to meet various needs. They are widely used in heavy industry, steel production facilities, railways, and warehouses. Among the defining features of heavy-load handling solutions high load capacity and durability stand out prominently.
Gantry Crane
Gantry cranes are heavy-duty industrial cranes capable of handling loads up to 500 tons without requiring building structures. Offered in single or double girder configurations, these cranes are ideal for container handling in ports, shipping zones, and warehouses due to their flexible movement capabilities. Semi-gantry cranes, integrated with crane position & collision monitoring systems, can operate effectively in confined spaces thanks to their compact designs.
Jib Crane
Jib cranes are fixed cranes typically equipped with rope or chain lifting mechanisms and have a lifting capacity of up to 20 tons. They are a preferred solution in warehouses, production facilities, and ports, especially where the use of overhead cranes is not feasible. With their freestanding or wall-mounted designs, these cranes are known for offering flexible and practical solutions within heavy load handling solutions.
What is the Wipelot Crane Safety System?
The Wipelot Crane Safety System is a comprehensive crane position monitoring and safety solution designed to ensure industrial crane safety. It tracks the real-time locations of the crane hook, load, and surrounding personnel or equipment. By precisely monitoring crane positions and detecting personnel or equipment entering the crane's dangerous zones, the system generates customized safety scenarios to enhance workplace safety.
Why Choose the Wipelot Crane Safety System?
Designed to meet the demanding requirements of heavy industries, the Wipelot Crane Safety System not only enhances overhead crane safety but also boosts crane operational efficiency.
If you aim to reduce risks, the system offers safety scenarios to address the complexities of crane movements and interactions with other equipment.
If you need a system integrated with inventory management, the system supports inventory tracking through additional modules, streamlining material flow.
If precise crane positioning is a priority, it enables 20 cm accuracy for monitoring crane locations via RTLS software.
If seamless integration matters, the system offers API-based integration with existing setups for fast and efficient use.
Features of the Crane Safety System
Wipelot’s Crane Tracking and Safety System enhances workplace safety and operational efficiency with advanced technology, adding value to industrial processes.
- Precision Positioning: Tracks crane movements with up to 20 cm accuracy, ensuring crane positioning reliability.
- Proximity Alerts: Prevents accidents by ensuring travelling crane safety through real-time alerts.
- 3D Position Visualization: Displays detailed tracking of crane positions on a software interface.
- Minimal Infrastructure: Easy setup without requiring complex installations.
- Real-Time Inventory Tracking: Facilitates workflow optimization with advanced tracking modules.
- Deceleration and Stopping: Detects hazardous proximities and slows down or stops crane movement to prevent accidents.
RTLS-Based Crane Safety and Operational Efficiency – FAQ
How does RTLS technology contribute to crane safety?
RTLS (Real-Time Location Systems) technology enhances crane safety by providing continuous tracking of crane hooks, loads, and nearby personnel. This allows for immediate detection of dangerous proximity, enabling automated responses like deceleration or emergency stopping to prevent collisions.
What makes Wipelot’s system suitable for heavy industry environments?
Wipelot’s system is built for rugged industrial settings. It delivers high-accuracy tracking (up to 20 cm), operates reliably in both indoor and outdoor environments, and integrates easily with existing safety and inventory systems, making it ideal for sectors like steel production, mining, and logistics.
Is infrastructure modification required to implement this system?
No major infrastructure changes are needed. Wipelot’s crane tracking system uses minimal hardware and can be deployed without disrupting existing workflows or requiring structural changes to facilities.
What kind of alerts does the system generate?
The system generates real-time alerts based on proximity between cranes, personnel, and equipment. These alerts are visualized through the RTLS software interface and can trigger automatic crane slowdown or stop actions when predefined thresholds are breached.
How does this solution improve operational efficiency in addition to safety?
In addition to preventing accidents, Wipelot’s solution helps streamline operations by offering real-time inventory tracking, 3D visualization of crane positions, and integration with material flow systems, leading to optimized task management and reduced downtime.
A New Era of Safety and Efficiency Through Innovation
By leveraging real-time location systems (RTLS), Wipelot enhances industrial crane safety and crane operational efficiency in heavy industry. These innovative solutions address both today’s needs and future operational goals, making industrial processes safer and more effective.
This advanced technological solution ensures seamless operations, boosts workplace safety, and adds significant value to heavy load handling systems. If you are seeking to prioritize safety and efficiency in your workplace, the Wipelot Crane Tracking and Safety System is the perfect choice.
Contact us to learn more and explore success stories from companies that have already transformed their operations with Wipelot.